
What is Polypropylene?
Polypropylene (PP) is a thermoplastic polymer belonging to the polyolefin family. At the molecular level, it consists of long chains of propylene monomers (C₃H₆) linked together. The arrangement of these molecules gives PP its distinctive properties. Most commercial PP is isotactic, meaning the methyl groups (CH₃) are arranged on the same side of the polymer backbone, creating a semi-crystalline structure.
This semi-crystalline nature is crucial to understanding PP's behavior. The crystalline regions provide strength and stiffness, while the amorphous (non-crystalline) regions contribute flexibility. This balanced internal structure creates a material with a unique combination of rigidity, flexibility, and durability that makes it appealing for various applications, including 3D printing.
In its natural state, PP is translucent to opaque with a milky appearance. It's one of the lightest thermoplastics available (with a density of about 0.90 g/cm³), which means it actually floats in water – a simple test to identify it.
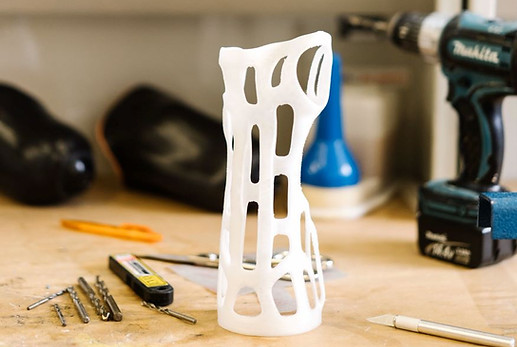
History of Polypropylene
Polypropylene has an interesting journey in the world of manufacturing and 3D printing:
Early development: Polypropylene was first polymerized in 1951 by Paul Hogan and Robert Banks of Phillips Petroleum, and independently by Italian chemist Giulio Natta in 1954. Natta and Karl Ziegler later won the Nobel Prize in Chemistry for their work on polymers. Commercial production began in the late 1950s.
Traditional manufacturing adoption: PP quickly became one of the most widely used plastics in conventional manufacturing due to its favorable properties and low cost. It's commonly used in everything from food containers and household items to automotive components and textiles.
Challenges in early 3D printing: Despite its prevalence in conventional manufacturing, PP was notably absent from the early days of consumer 3D printing. While materials like ABS and PLA became staples of FDM (Fused Deposition Modeling) printing in the 2000s and early 2010s, PP remained elusive due to several technical challenges:
-
Significant warping during cooling
-
Poor layer adhesion
-
Difficulty adhering to print beds
-
Narrow processing window
Breakthrough developments: Around 2015-2017, several filament manufacturers began introducing specially formulated PP filaments designed to address these challenges. These formulations often included additives to improve printability while maintaining PP's desirable characteristics.
Current status: Today, while still not as common as PLA, PETG, or ABS, polypropylene filaments have carved out a niche in the 3D printing ecosystem. Several major filament brands now offer PP options, and as printer technology has advanced with better temperature control and build plate solutions, PP has become more accessible to advanced users.
Industrial adoption: In industrial 3D printing, especially for functional prototypes and end-use parts, PP has gained more traction. Companies in automotive, consumer goods, and medical fields have been exploring PP for applications where its chemical resistance and durability are advantageous.
Advantages of Polypropylene for 3D Printing
Polypropylene offers several distinctive advantages that make it valuable for specific applications:
Chemical resistance: PP exhibits exceptional resistance to a wide range of chemicals, including acids, bases, solvents, and oils. This makes it ideal for parts that will come into contact with chemicals or fuels.
Fatigue resistance: PP has outstanding resistance to repeated bending and flexing. It can undergo thousands of flex cycles without breaking, making it perfect for living hinges (thin sections designed to flex repeatedly).
Food safety: Most PP filaments are food-safe (though specific grades should be verified), making them suitable for items like custom containers, utensils, or food processing tools.
Lightweight: With a density of approximately 0.90 g/cm³, PP is one of the lightest 3D printable thermoplastics. This makes it valuable for applications where weight is a concern.
Water resistance: PP is naturally hydrophobic and won't absorb water, even when submerged for extended periods. This makes it suitable for aquatic applications and outdoor use.
Temperature resistance: With a melting point around 160-170°C, PP can withstand moderately high temperatures, making it more heat-resistant than PLA (which begins to soften around 60°C).
Toughness and impact resistance: PP offers a good balance of rigidity and impact strength. It's less brittle than PLA and can absorb impacts without shattering.
Recyclability: PP is widely recycled (recycle code 5) in many municipal recycling programs.
Electrical insulation: PP has excellent electrical insulating properties, making it suitable for electronic enclosures and components.
Cost-effectiveness: In conventional manufacturing, PP is one of the least expensive plastics. While specialized 3D printing filaments command a premium, PP is still relatively economical compared to engineering filaments.
Disadvantages of Polypropylene
Despite its advantages, PP presents several significant challenges for 3D printing:
Extreme warping: PP has one of the highest shrinkage rates among common 3D printing materials (1.5-2.5% linear shrinkage). This causes severe warping and curling, especially in parts with large flat surfaces.
Poor bed adhesion: PP's low surface energy and non-polar nature make it notoriously difficult to get it to stick to print beds. It doesn't adhere well to most common build surfaces.
Layer adhesion issues: PP has relatively poor layer-to-layer bonding compared to materials like PLA or PETG, which can result in weaker Z-axis strength.
Narrow processing window: PP has a relatively narrow temperature range where it prints well. Too cool, and layers won't bond; too hot, and the material degrades quickly.
Limited printability of fine details: PP isn't ideal for prints requiring fine details or sharp corners due to its flowing nature when molten and high shrinkage.
UV sensitivity: Unmodified PP degrades when exposed to ultraviolet light for extended periods, becoming brittle and discolored.
Limited color options: Due to its more specialized nature, PP filaments are available in fewer colors compared to mainstream materials like PLA.
Print speed limitations: PP typically requires slower print speeds to ensure proper layer adhesion and to manage cooling-related issues.
Difficult to post-process: PP doesn't easily accept paints or adhesives without special surface treatments due to its low surface energy.
Filament variability: The quality and printability of PP filaments can vary significantly between manufacturers, making it somewhat unpredictable.
3D Printer Requirements for Polypropylene
Successfully printing with polypropylene demands specific printer capabilities:
Enclosed printing chamber: An enclosed print area is highly recommended to maintain a consistent ambient temperature and prevent drafts, which can cause layer separation and warping.
Heated print bed: A bed capable of reaching 85-100°C is essential. Some users report success with even higher temperatures (up to 110°C) for larger parts.
Hot end temperature capability: PP typically prints at 230-260°C, so your printer must be able to reliably maintain these temperatures. An all-metal hot end is recommended for regular PP printing.
Build surface considerations:
-
PP-specific surfaces like Airwolf's Wolfbite Nitro adhesive
-
Polypropylene tape (specialized tape made from PP itself)
-
GeckTek or BuildTak surfaces with PP-compatible adhesive
-
Glass with a thin layer of glue stick (though adhesion may still be challenging)
-
Textured polypropylene build plates that leverage similar-to-similar adhesion
Cooling system: Controlled cooling is crucial for PP. Most users find that minimal cooling (0-20% fan) yields the best results, but this requires a fan that can be precisely controlled.
Printer frame and component quality: Given PP's tendency to warp, a rigid printer frame helps maintain dimensional accuracy by resisting the forces exerted as the material cools and contracts.
Direct drive extruder (recommended): While not strictly necessary, a direct drive extruder provides better control over retraction and extrusion with PP, which can be slightly flexible in filament form.
Filament dry storage and/or drying capability: While PP is less hygroscopic than many filaments, keeping it dry still improves print quality.
Material Properties of Polypropylene
Bed Temp | 85-100°C |
Density | 0.9 g/cm3 |
Heated Bed | Not Required |
Coefficient of Thermal Expansion | 150 µm/m-°C |
Ultimate Strength | 32 MPa |
Extruder Temp | 220-250°C |
Printability | Difficult |
Max Service Temp | 100°C |
Stiffness | Low-Medium |
Durability | High |
How to Print with Polypropylene - Tips and Tricks
To achieve the best results when printing with polypropylene, consider these practical tips:
Optimal print settings:
-
Nozzle temperature: 230-260°C (start at 245°C and adjust based on results)
-
Bed temperature: 85-100°C (95°C is a good starting point)
-
Print speed: 20-40 mm/s (slower than typical PLA speeds)
-
Layer height: 0.2-0.3mm is typically more successful than very fine layers
-
Cooling: Minimal fan speed (0-20%) or no cooling for most parts
-
First layer: Print very slow (10-15 mm/s) and slightly hotter for better adhesion
Bed adhesion strategies:
-
Apply PP-specific adhesives like Wolfbite Nitro
-
Use PP tape on the build surface (using the same material creates natural adhesion)
-
For smaller parts, a wide brim (8-10mm) or raft can significantly improve success rates
-
Ensure the bed is meticulously level and clean before printing
-
Some users report success with a light misting of hairspray on a glass bed heated to 100°C
Managing warping:
-
Design parts with rounded corners on the first layer to reduce lifting
-
Minimize large flat areas in contact with the bed when possible
-
Use a draft shield (a single-wall perimeter printed around your part)
-
Print in an enclosure with elevated ambient temperature (40-50°C)
-
Consider orienting parts to minimize the footprint on the build plate
Optimizing layer adhesion:
-
Slight under-extrusion (95-97% flow rate) can sometimes improve layer bonding with PP
-
Ensure the printing environment is draft-free
-
Print at the higher end of the temperature range for better layer fusion
-
Consider increasing line width to 120% of nozzle diameter for stronger parts
Storage and filament care:
-
While PP is less hygroscopic than many filaments, store it in airtight containers with desiccant
-
Before critical prints, drying at 60-70°C for 2-4 hours can improve results
-
Handle the filament carefully as it can be slightly more flexible than other filaments
Design considerations for PP:
-
Leverage PP's flexibility by designing intentional living hinges (thin areas meant to flex repeatedly)
-
Increase wall thickness compared to PLA designs to compensate for potentially weaker layer bonding
-
Consider designing snap-fits and clips that take advantage of PP's flexibility and fatigue resistance
-
Allow tolerances for shrinkage in precision parts (approximately 2%)
Post-processing techniques:
-
Mechanical finishing works well (sanding, drilling, cutting)
-
For joining parts, consider ultrasonic welding or heat staking if equipment is available
-
For adhesion, surface treatment may be necessary (flame treatment, corona discharge, or chemical primers)
-
PP doesn't easily accept paint without surface preparation (primers specifically designed for polyolefins can help)
Environmental Considerations
PP presents an interesting environmental profile:
Recyclability: PP is widely recycled in many municipal programs (recycle code 5). High-quality PP can typically go through several recycling cycles before significant degradation occurs.
Energy efficiency: The relatively low processing temperatures of PP (compared to materials like nylon or PEEK) mean lower energy consumption during both manufacturing and 3D printing.
Durability and longevity: PP parts tend to last longer than those made from some other materials, potentially reducing replacement frequency and overall material consumption.
Non-biodegradability: Like most conventional plastics, PP does not biodegrade in natural environments and will persist for many decades if not properly disposed of or recycled.
Production footprint: As a petroleum-derived plastic, PP production requires fossil fuel resources. However, it's considered more resource-efficient to produce than many other plastics due to its lightweight nature (more parts per kg of raw material).
Potential for bio-based alternatives: Research into bio-based polypropylene made from renewable resources is ongoing, though not yet widely commercialized for 3D printing.
Recyclability of printed parts: While theoretically recyclable, many recycling facilities may not accept 3D printed PP parts due to potential additives and the small quantities typically involved.
Polypropylene vs. Other Common Filaments
To better understand PP's place in the 3D printing material landscape, it's helpful to compare it directly with other popular filaments:
PP vs. PLA:
-
PP is significantly more durable, flexible, and chemically resistant
-
PLA is much easier to print, with minimal warping and excellent detail reproduction
-
PP offers better temperature resistance and durability in moist environments
-
PLA is biodegradable and made from renewable resources, unlike petroleum-based PP
PP vs. PETG:
-
PETG has better layer adhesion and less warping than PP
-
PP offers better chemical resistance, especially to bases and some solvents
-
PETG typically produces parts with better surface finish
-
PP is more suitable for applications requiring repeated flexing
PP vs. ABS:
-
Both materials warp significantly, but PP typically warps more
-
PP has superior chemical resistance compared to ABS
-
ABS can be smoothed with acetone; PP lacks an equivalent easy smoothing process
-
PP is more environmentally friendly to print (no styrene emissions)
PP vs. TPU:
-
TPU is significantly more elastic and has better layer adhesion
-
PP retains its shape better after flexing and has higher temperature resistance
-
PP offers better chemical resistance than most TPU variants
-
TPU is easier to print with fewer bed adhesion issues
PP vs. Nylon:
-
Nylon has superior strength and wear resistance
-
PP offers better chemical resistance, especially to bases
-
Nylon absorbs moisture much more readily than PP
-
PP is generally easier to print than nylon (lower temperatures, less moisture sensitivity)
Not right for you? Learn about other materials here.
