
What is PPE Glass Fiber?
PPE (Polyphenylene Ether) is a high-performance engineering thermoplastic that belongs to the family of polyethers. When reinforced with glass fibers, it creates a composite material that combines the inherent properties of PPE with the strength enhancement provided by glass fiber reinforcement. The glass fibers typically make up between 10-30% of the material composition, giving it significantly improved mechanical properties compared to pure PPE.
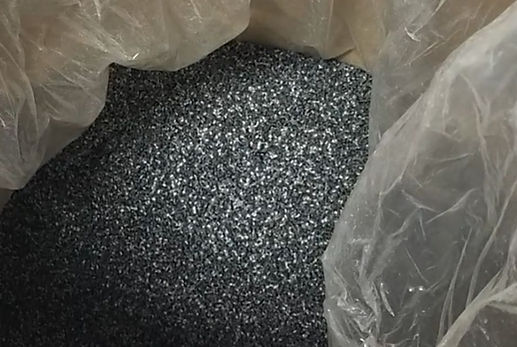
History of PPE Glass Fiber
PPE was first developed by General Electric in the 1960s under the trade name Noryl. However, its adaptation for 3D printing is relatively recent, emerging in the mid-2010s as part of the broader trend toward engineering-grade materials in additive manufacturing.
The integration of glass fibers with PPE for 3D printing applications arose from the need for printed parts with enhanced mechanical properties, particularly in industries requiring functional prototypes and end-use parts. Companies like Stratasys, SABIC, and BASF have been at the forefront of commercializing these materials for industrial 3D printing applications.
Advantages of PPE Glass Fiber for 3D Printing
PPE glass fiber offers several significant advantages that make it valuable for specific applications:
Thermal Stability: PPE has excellent dimensional stability at high temperatures, with heat deflection temperatures that can exceed 200°C when properly reinforced. This makes it suitable for applications involving elevated temperatures.
Chemical Resistance: The material demonstrates good resistance to many chemicals, acids, and bases, making it useful in environments where chemical exposure is common.
Mechanical Strength: The addition of glass fibers dramatically improves tensile strength, flexural modulus, and impact resistance compared to unfilled PPE.
Dimensional Stability: PPE has low moisture absorption (typically less than 0.1%), resulting in minimal warping or dimension changes over time, even in humid environments.
Flame Retardancy: Many PPE formulations offer inherent flame retardant properties without additives, meeting UL94 V-0 standards in some cases.
Electrical Properties: PPE provides excellent electrical insulation properties, making it suitable for electrical and electronic components.
Disadvantages of PPE Glass Fiber
Despite its advantages, PPE glass fiber has several limitations to consider:
Processing Challenges: The high processing temperature (often 260-320°C) requires specialized 3D printers with high-temperature capabilities.
Abrasiveness: The glass fiber content is highly abrasive on printer nozzles, leading to accelerated wear and the need for hardened steel or ruby nozzles.
Surface Finish: Glass fiber reinforced materials typically have a rougher surface finish compared to unfilled materials, which may require post-processing.
Cost: PPE glass fiber filaments and powders are significantly more expensive than standard 3D printing materials like PLA or ABS, often costing 5-10 times more.
Limited Color Options: Due to its specialized nature, PPE glass fiber materials are typically available in a limited color range (often black, natural, or gray).
Brittleness: While strong, glass fiber reinforced materials can be more brittle than their unreinforced counterparts, potentially leading to unexpected part failures under certain stress conditions.
3D Printer Requirements for PPE Glass Fiber
Printing with PPE glass fiber demands specific hardware capabilities:
High-Temperature Components: Extruders must handle temperatures of 300°C or higher, with heated chambers or build plates maintaining 100-150°C.
Hardened Components: Hardened steel nozzles or ruby/sapphire nozzles are necessary to resist the abrasive wear from glass fibers.
Enclosed Chamber: A fully enclosed and temperature-controlled build chamber helps manage the cooling rate and prevent warping.
Robust Extrusion System: A high-torque extruder is needed as glass fiber materials are more difficult to push through the nozzle.
Specialized Build Surfaces: High-temperature build surfaces with appropriate adhesion solutions (often polyimide tape or specialized adhesives) are required.
Advanced Cooling: Controlled cooling systems help manage the thermal gradients to prevent warping and layer delamination.
Material Properties of PPE Glass Fiber
Bed Temp | 65-80°C |
Density | 1.3 g/cm3 |
Heated Bed | Required |
Coefficient of Thermal Expansion | 28 µm/m-°C |
Ultimate Strength | 93 MPa |
Extruder Temp | 280-320°C |
Printability | Very Easy |
Max Service Temp | 80°C |
Stiffness | Very High |
Durability | High |
Applications of Printing with PPE Glass Fiber
PPE glass fiber excels in several application areas:
Aerospace: Components requiring flame retardancy and high thermal stability
Automotive: Under-hood components where heat resistance is crucial
Electrical: Insulating components, connector housings, and electrical enclosures
Industrial: Tooling applications, jigs, and fixtures that need dimensional stability
Medical: Equipment housing and non-implantable devices requiring sterilization
Common Post-Processing Operations with PPE Glass Fiber
Parts printed with PPE glass fiber often benefit from several post-processing techniques:
Annealing: Heating parts to just below glass transition temperature (typically 140-160°C) for several hours can relieve internal stresses and improve mechanical properties.
Surface Finishing: Sanding, vapor smoothing with appropriate solvents, or coating can improve the surface finish.
Machining: PPE glass fiber parts can be drilled, tapped, and machined using standard tools, though the glass fiber content will accelerate tool wear.
Not right for you? Learn about other materials here.
