
What is TPU?
Thermoplastic Polyurethane (TPU) is a unique class of thermoplastic elastomer that combines the processing advantages of thermoplastics with the performance properties of rubber. Unlike rigid filaments such as PLA or ABS, TPU creates flexible, elastic parts that can stretch, compress, and bend without breaking.
To understand TPU, imagine a material that sits at the intersection of plastic and rubber. When you print with TPU, you're essentially creating objects that have rubber-like properties but can be processed using standard 3D printing equipment. This special combination makes TPU incredibly valuable for applications where flexibility, impact resistance, and wear resistance are crucial.
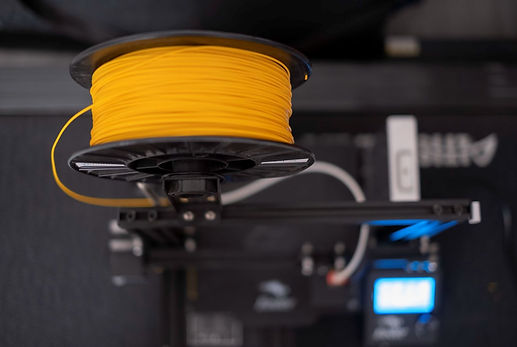
History of TPU
The story of polyurethane begins in the late 1930s with Otto Bayer's groundbreaking work at I.G. Farben in Germany. Bayer developed the basic diisocyanate polyaddition process, creating the foundation for all polyurethane chemistry. However, the earliest polyurethanes were thermosets (materials that once cured, cannot be melted again).
The transformation to thermoplastic polyurethanes came in the 1950s and 1960s as chemists developed methods to create polyurethanes without the permanent cross-linking that made earlier versions thermosets. This breakthrough allowed the material to be melted and reformed multiple times – a critical requirement for extrusion-based processes like 3D printing.
Commercial TPU saw widespread adoption in various industries throughout the 1970s and 1980s for applications ranging from automotive parts to footwear. Companies like B.F. Goodrich (now part of Lubrizol), BASF, and Bayer MaterialScience (now Covestro) became major producers of TPU resins.
TPU made its entry into the 3D printing world relatively recently. While early desktop 3D printing (circa 2009-2012) focused almost exclusively on rigid materials like PLA and ABS, the growing maturity of the technology around 2014-2015 opened the door to more specialized materials. Companies like NinjaTek and Fenner Drives introduced some of the first commercially successful TPU filaments for 3D printing with their Ninjaflex and eSUN brands, respectively.
As printer technology evolved to handle flexible materials better (particularly with the development of direct drive extruders and optimized feed paths), TPU became increasingly accessible to hobbyists and professionals alike. Today, nearly every major filament manufacturer offers at least one TPU variant, with countless formulations available across a spectrum of flexibility, from slightly flexible to extremely soft and rubber-like.
Advantages of TPU for 3D Printing
TPU offers several compelling advantages that make it a valuable material for specific applications:
Exceptional Flexibility and Elasticity: The most obvious benefit of TPU is its ability to flex, stretch, and then return to its original shape. Depending on the specific formulation, TPU can stretch 200-700% before breaking and then recover with minimal permanent deformation. This property is particularly valuable for parts that need to flex repeatedly or absorb impact forces.
Outstanding Impact Resistance: TPU excels at absorbing and dissipating energy from impacts. Drop a rigid plastic part and it might crack or shatter; drop a TPU part and it's likely to bounce. This makes TPU ideal for protective cases, bumpers, and shock-absorbing components.
Excellent Abrasion Resistance: TPU withstands friction and wear remarkably well, often outlasting rigid plastics in applications involving sliding, rubbing, or repeated contact. This durability makes it perfect for wheels, tire treads, and other parts subject to constant wear.
Chemical Resistance: TPU shows good resistance to many oils, greases, and some chemicals. While it's not universally chemical-resistant, it handles exposure to petroleum products and many solvents better than some other 3D printing materials.
UV and Weather Resistance: Many TPU formulations offer good resistance to degradation from UV light and weathering, making them suitable for outdoor applications.
Vibration Dampening: The viscoelastic nature of TPU allows it to absorb vibrations, making it useful for isolating electronic components, reducing noise, or damping mechanical vibrations.
Low-Temperature Performance: Unlike some materials that become brittle when cold, many TPU formulations retain their flexibility even at temperatures well below freezing.
Layer Adhesion: TPU typically exhibits excellent layer adhesion, creating strong bonds between printed layers that contribute to overall part durability and water/air tightness.
Biocompatibility: Some specialized TPU formulations are biocompatible, allowing for applications that involve skin contact or even temporary internal use (with appropriate medical-grade materials).
Disadvantages of TPU
Despite its impressive properties, TPU presents several challenges that anyone considering this material should understand:
Printing Speed Limitations: Due to its flexible nature, TPU must be printed significantly slower than rigid materials – often at half the speed or less. This means longer print times for comparable parts.
Stringing and Oozing: TPU's elastic nature makes it prone to stringing and oozing during printing, as the material stretches rather than making clean breaks during retraction moves. This can lead to stringy prints that require post-processing cleanup.
Precision Challenges: The flexible nature of TPU makes it difficult to achieve the same level of dimensional precision as rigid materials. Fine details and sharp corners may not reproduce as accurately.
Moisture Sensitivity: Like many filaments, TPU is hygroscopic, meaning it absorbs moisture from the air. Wet TPU filament can cause popping, bubbling, and reduced part quality. Proper storage and drying are essential.
Bridging Limitations: TPU struggles with bridging (printing horizontally over gaps) due to its flexible nature. Designs often need to be modified to minimize bridging requirements.
Support Structure Complications: Removing support structures from TPU prints can be challenging – the flexibility that makes TPU valuable also makes it difficult to break away supports cleanly without damaging the main part.
Bed Adhesion Balancing Act: While TPU generally adheres well to build plates, finding the right balance can be tricky. Too much adhesion makes parts difficult to remove, while too little leads to failed prints.
Cost Considerations: TPU filament typically costs 2-3 times more than standard PLA filament, making it a more expensive option for large projects.
Limited Color Options: While the situation is improving, TPU typically offers fewer color options than more common materials like PLA or PETG.
Printer Compatibility Issues: Not all 3D printers can effectively handle TPU, particularly those with Bowden extruders or long, unconstrained filament paths.
3D Printer Requirements for TPU
Successfully printing with TPU requires specific printer capabilities. Here's what to look for:
Direct Drive Extruder: The most critical feature for TPU printing. Direct drive extruders (where the extruder motor is mounted directly above the hotend) provide much better control over the flexible filament than Bowden systems, which push the filament through a long tube. Bowden setups often struggle with TPU because the flexible filament can buckle and jam in the tube.
Constrained Filament Path: Any gaps in the filament path where the flexible material could escape or buckle will cause problems. Look for printers with fully constrained filament paths from the drive gear to the hotend.
Adjustable Extruder Tension: The ability to fine-tune the pressure on the filament is important for TPU. Too much pressure can deform the filament and cause feeding issues, while too little won't provide enough grip.
Moderate Print Speeds: Your printer should allow for slow, controlled printing, typically in the range of 15-30 mm/s for TPU (compared to 40-80 mm/s for rigid materials).
Controlled Cooling: Adjustable part cooling is important for TPU. Depending on the specific formulation and part geometry, you may need to reduce cooling to improve layer adhesion or increase it to improve surface details.
Heated Bed: While not absolutely essential for all TPU formulations, a heated bed (typically set to 40-60°C) improves adhesion for the first layer and helps prevent warping.
Level Build Surface: A well-leveled build surface is even more critical for TPU than for rigid materials, as the flexible nature of TPU can accentuate any leveling issues.
Retraction Control: Fine control over retraction settings helps manage stringing and oozing, common challenges with TPU printing.
Material Properties of TPU
Bed Temp | 50-60°C |
Density | 1.16 g/cm3 |
Heated Bed | Not Required |
Coefficient of Thermal Expansion | 100 µm/m-°C |
Ultimate Strength | 39 MPa |
Extruder Temp | 220-250°C |
Printability | Durability |
Max Service Temp | 52°C |
Stiffness | Low |
Durability | High |
Designing for TPU
Designing specifically for TPU requires understanding how the material's properties affect what you can and cannot do:
Wall Thickness: TPU parts generally need thicker walls than rigid plastic equivalents. For flexible sections, 1.2-2.0mm thickness often works well, depending on the desired flexibility.
Minimize Overhangs and Bridges: TPU struggles with overhangs and bridges. Design parts to minimize these features or incorporate supports where necessary.
Self-Supporting Angles: While rigid materials can often print overhangs up to 45-60 degrees without support, TPU is more limited – aim to keep overhangs under 30-40 degrees.
Support Design: When supports are necessary, design them with greater spacing and easier removal in mind. Consider using water-soluble supports (like PVA) for complex geometries if your printer supports dual extrusion.
Tolerance Adjustments: TPU parts often require different tolerances than rigid parts due to the material's flexibility and slight expansion after extrusion. For press-fit designs, tighter tolerances are typically needed.
Functional Flexibility: When designing intentionally flexible sections, consider using honeycomb or gyroid internal structures rather than solid infill to achieve controlled, predictable flexibility.
Living Hinges: TPU excels at creating living hinges (thin flexible sections connecting more rigid parts). Design these with 0.4-0.8mm thickness for optimal flexibility and durability.
Surface Textures: TPU reproduces surface textures well and can be designed with intentional textures to improve grip or tactile feel.
Print Orientation: The orientation of your part can significantly affect its flexibility. Layer lines perpendicular to the direction of flex will create a more flexible part than layer lines parallel to the flex direction.
How to print with TPU - Tips and Tricks
These practical tips can help improve your success rate with TPU:
Start with Firmer TPU Varieties: If you're new to flexible filament printing, begin with firmer TPU formulations (Shore A 95 or Shore D 40-60) as they're more forgiving and easier to print.
Print Test Pieces First: Before committing to large prints, test your settings with small calibration pieces to dial in the right parameters for your specific machine and filament.
Slow Down: When in doubt, slow down your print speed. Many TPU printing issues can be resolved simply by printing more slowly.
Dry Your Filament: TPU is hygroscopic and performs poorly when moisture-laden. Dry your filament at 45-50°C for 4-6 hours before critical prints.
Prevent Dust Accumulation: TPU's tacky surface attracts dust. Use filament cleaners or dust filters, and store filament in clean, sealed containers.
Clean Your Build Plate Thoroughly: Any oils or residues on the build surface can affect adhesion. Clean with isopropyl alcohol before printing.
Consider a Direct Drive Upgrade: If you have a Bowden extruder printer but want to use TPU regularly, consider upgrading to a direct drive extruder system.
Mind Your Retraction: Start with minimal retraction settings and increase gradually. Too much retraction is a common cause of TPU feeding problems.
Use Controlled Cooling: Rather than blasting your part with cooling, use moderate fan speeds to balance layer adhesion with feature detail.
Try Different Bed Materials: Different TPU formulations adhere differently to various surfaces. Experiment with BuildTak, PEI, glass with glue stick, or specialty surfaces to find what works best for your specific filament.
Print Multiple Parts Separately: Rather than printing multiple small parts in one job, consider printing them one at a time to reduce stringing and travel issues.
Optimize Travel Paths: In your slicer, configure travel paths to minimize crossing over the print, which helps reduce stringing.
Environmental and Safety Considerations
As with any 3D printing material, there are environmental and safety factors to consider with TPU:
Emissions During Printing: TPU generally produces fewer potentially harmful volatile organic compounds (VOCs) than materials like ABS, but proper ventilation is still recommended.
Biodegradability: Standard TPU is not biodegradable and will persist in the environment for many years. However, some manufacturers now offer biodegradable TPU variants.
Recyclability: TPU is technically recyclable, though the infrastructure for recycling 3D printing waste is still developing in most areas.
End-of-Life Considerations: Due to its durability, TPU products have a long useful life, which can offset some environmental concerns.
Material Safety: Most commercial TPU filaments are considered non-toxic in solid form, but as with all 3D printing materials, avoid direct food contact unless using specifically food-safe grades.
Biocompatibility: For applications involving skin contact or medical use, only use TPU filaments specifically certified for these purposes.
Applications of TPU
The unique properties of TPU make it ideal for specific applications where rigid materials would fail:
Protective Cases and Bumpers: Phone cases, camera bumpers, drone landing gear, and other protective components that need to absorb impact.
Wearable Items: Watch bands, fitness tracker straps, orthotic inserts, and other body-contact items benefit from TPU's comfortable feel and durability.
Wheels and Tires: RC car tires, robot wheels, and other rolling components that need traction and shock absorption.
Gaskets and Seals: Custom gaskets, O-rings, and sealing components for mechanical assemblies or waterproofing.
Vibration Dampeners: Motor mounts, speaker isolators, and other components designed to reduce vibration transmission.
Grippy Surfaces and Handles: Tool grips, ergonomic handles, and non-slip pads or feet for devices.
Flexible Connectors: Cable strain relief, flexible joints, and connection points between rigid components.
Functional Springs and Elastic Components: Custom spring elements, elastic bands, and tension components.
Medical and Prosthetic Components: Custom-fit prosthetic interfaces, anatomical models for surgical planning, and rehabilitation devices.
Artistic and Fashion Applications: Flexible jewelry, textile-like structures, and decorative elements that incorporate movement.
What is Glass-Filled TPU?
Glass-filled TPU (Thermoplastic Polyurethane) is a composite 3D printing filament that combines TPU, a flexible, rubber-like material, with glass fibers to enhance its properties. The addition of glass fibers significantly improves the mechanical strength and stiffness of the material while maintaining its flexibility and elasticity to some degree.
Increased Strength and Stiffness: The glass fibers added to the TPU make the material stronger and more rigid, improving its tensile strength and impact resistance compared to regular TPU. This makes it more suitable for applications where both flexibility and mechanical strength are needed.
Improved Wear Resistance: Glass-filled TPU has better abrasion resistance than regular TPU, making it more durable in high-wear applications such as gears, wheels, and other moving parts. The fibers help reduce wear and tear when in contact with other surfaces.
Higher Dimensional Stability: The addition of glass fibers reduces the shrinkage and warping that is typically seen with flexible filaments like TPU. This makes it easier to print with, particularly for more complex designs that require stability.
Enhanced Thermal Resistance: Glass-filled TPU tends to have better heat resistance than standard TPU, allowing it to perform in environments with moderate temperatures (up to 80-100°C) without deforming or losing its structural integrity.
Reduced Flexibility: While glass-filled TPU still retains some degree of flexibility, the addition of glass fibers makes it less flexible than regular TPU. The material becomes stiffer, making it more suitable for applications that require a balance of flexibility and rigidity.
Smoother Surface Finish: The glass fibers in the filament often give printed parts a smoother surface compared to regular TPU, reducing the visibility of layer lines and providing a more refined finish.
Not right for you? Learn about other materials here.
